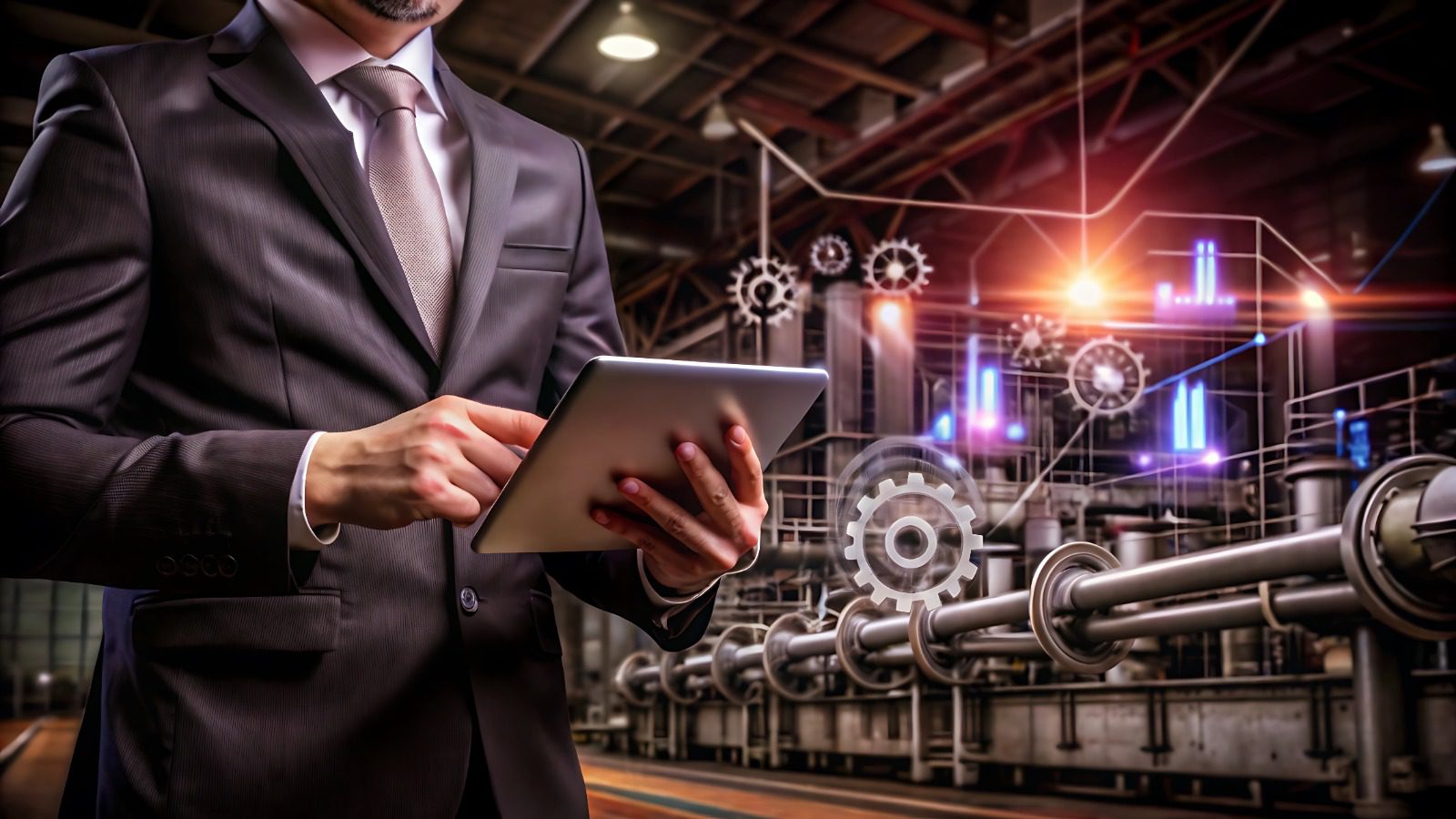
Production Management: Optimizing Manufacturing Processes
Introduction
In the dynamic landscape of manufacturing, production management plays a pivotal role in ensuring that operations run smoothly, efficiently, and cost-effectively. As industries evolve and competition intensifies, manufacturers must adopt strategies to optimize their production processes. Effective production management not only streamlines operations but also enhances product quality, reduces waste, and improves overall profitability. This blog delves into the technical aspects of production management, focusing on how to optimize manufacturing processes through strategic planning, technology integration, and continuous improvement.
1. Understanding Production Management
Production management encompasses the planning, coordination, and control of manufacturing processes. It involves overseeing the entire production cycle, from raw material procurement to finished product delivery. Key components of production management include:
- Production Planning: Determining what, when, and how much to produce based on demand forecasts.
- Scheduling: Allocating resources and setting timelines for production activities.
- Quality Control: Ensuring products meet specified quality standards.
- Inventory Management: Monitoring stock levels and managing material flows.
By effectively managing these components, manufacturers can optimize their production processes, minimize costs, and respond quickly to market changes.
2. The Importance of Production Optimization
Production optimization refers to the process of improving manufacturing operations to maximize efficiency, quality, and profitability. The importance of optimizing production processes cannot be overstated, as it leads to several benefits:
- Increased Efficiency: Streamlined operations result in faster production cycles and reduced lead times.
- Cost Reduction: By minimizing waste and optimizing resource utilization, manufacturers can lower production costs.
- Enhanced Quality: Consistent quality control measures help maintain product standards, reducing defects and returns.
- Better Flexibility: An optimized production process enables manufacturers to adapt quickly to changing market demands and customer preferences.
3. Key Challenges in Production Management
While optimizing production processes is essential, manufacturers often face several challenges, including:
- Demand Fluctuations: Variability in customer demand can lead to overproduction or stockouts.
- Resource Constraints: Limited availability of materials, labor, or equipment can hinder production efficiency.
- Complex Supply Chains: Managing multiple suppliers and logistics can complicate inventory management and production scheduling.
- Quality Assurance: Ensuring consistent product quality while minimizing defects requires rigorous control measures.
4. Leveraging ERP Systems for Production Management
Enterprise Resource Planning (ERP) systems are crucial for effective production management, as they integrate various business functions into a single platform. An ERP system provides manufacturers with real-time data and insights to optimize production processes.
4.1. Centralized Data Management
ERP systems consolidate data from different departments, allowing for better visibility and decision-making. Manufacturers can access accurate information about inventory levels, production schedules, and demand forecasts in real-time.
4.2. Production Planning and Scheduling
ERP solutions offer advanced planning and scheduling tools that help manufacturers optimize production processes. Features such as Material Requirements Planning (MRP) and Capacity Planning enable manufacturers to:
- Calculate material needs based on production schedules.
- Allocate resources efficiently to meet demand.
- Adjust schedules dynamically to respond to changes in demand or resource availability.
4.3. Quality Management
ERP systems facilitate quality management by integrating quality control processes into production workflows. Manufacturers can set quality standards, track defects, and implement corrective actions seamlessly.
4.4. Inventory Optimization
With an ERP system, manufacturers can gain real-time visibility into inventory levels, leading to better inventory management. Features such as Just-In-Time (JIT) inventory management can help reduce holding costs and minimize waste.
5. Best Practices for Optimizing Manufacturing Processes
To achieve production optimization, manufacturers should implement the following best practices:
5.1. Implement Lean Manufacturing Principles
Lean manufacturing focuses on minimizing waste while maximizing value. Key principles include:
- Value Stream Mapping: Identify and analyze the flow of materials and information to eliminate non-value-added activities.
- Continuous Improvement (Kaizen): Foster a culture of continuous improvement by encouraging employees to identify and implement process enhancements.
5.2. Embrace Automation
Automation technologies, such as robotics and machine learning, can significantly enhance production efficiency. By automating repetitive tasks, manufacturers can reduce human error, increase production speed, and improve safety.
5.3. Invest in Training and Development
Providing ongoing training for employees is essential for optimizing production processes. Well-trained staff are more likely to identify inefficiencies and contribute to process improvements.
5.4. Utilize Data Analytics
Leveraging data analytics tools within an ERP system can provide valuable insights into production performance. Manufacturers can analyze historical data to identify trends, forecast demand, and make data-driven decisions.
5.5. Collaborate with Suppliers
Building strong relationships with suppliers can enhance production efficiency. Collaborative planning and communication with suppliers ensure that materials are delivered on time and meet quality standards.
Let's discuss, we are here to accelerate your business and ROI
6. Measuring Production Performance
To determine the effectiveness of production optimization efforts, manufacturers should establish Key Performance Indicators (KPIs) that provide insights into production performance. Common KPIs include:
- Overall Equipment Effectiveness (OEE): Measures the efficiency of manufacturing equipment by considering availability, performance, and quality.
- Production Cycle Time: The total time taken to complete a production cycle, from raw material procurement to finished goods delivery.
- Scrap Rate: The percentage of products that do not meet quality standards and must be discarded.
- On-Time Delivery Rate: Measures the percentage of orders delivered on time to customers.
Regularly monitoring these KPIs enables manufacturers to assess the effectiveness of their production optimization strategies and identify areas for improvement.
7. Case Studies of Successful Production Optimization
7.1. Toyota Production System
The Toyota Production System (TPS) is a renowned example of successful production optimization. By implementing lean manufacturing principles and focusing on continuous improvement, Toyota has been able to reduce waste, enhance quality, and increase efficiency.
Key elements of TPS include:
- Just-In-Time (JIT) Production: Producing only what is needed when it is needed, reducing inventory costs.
- Jidoka (Automation with a Human Touch): Empowering employees to stop production lines in case of defects, ensuring quality at the source.
7.2. Procter & Gamble (P&G)
P&G has successfully optimized its manufacturing processes by leveraging advanced analytics and automation. By implementing data-driven decision-making, P&G has improved forecasting accuracy, reduced production costs, and enhanced product quality.
8. Future Trends in Production Management
The manufacturing industry is continually evolving, and several trends are shaping the future of production management:
8.1. Industry 4.0
Industry 4.0 refers to the fourth industrial revolution, characterized by the integration of smart technologies such as IoT, AI, and big data analytics into manufacturing processes. This trend enables manufacturers to achieve greater efficiency, flexibility, and customization.
8.2. Sustainability
Sustainability is becoming a critical consideration in production management. Manufacturers are increasingly adopting eco-friendly practices, such as reducing energy consumption, minimizing waste, and utilizing sustainable materials.
8.3. Advanced Robotics
Advancements in robotics technology are enhancing automation capabilities in manufacturing. Collaborative robots (cobots) are designed to work alongside human operators, increasing efficiency and safety on the production floor.
9. Conclusion
Optimizing manufacturing processes through effective production management is essential for manufacturers seeking to enhance efficiency, reduce costs, and improve product quality. By leveraging ERP systems and implementing best practices, organizations can achieve significant improvements in their production operations.
Collaborating with the Best ERP Solution Provider in Hyderabad is crucial for manufacturers looking to implement effective production management strategies. Partnering with the Best ERP Partner ensures access to top-notch solutions and support, while the Best ERP services provider can guide organizations in their optimization efforts. By investing in #1 Cloud-Based ERP Software and #1 Cloud-Based ERP System, manufacturers can streamline their processes and drive sustainable growth in a competitive market.
FAQs
Production management involves planning, coordinating, and controlling manufacturing processes to ensure efficient operations and high-quality products.
Optimizing manufacturing processes leads to increased efficiency, cost reduction, enhanced quality, better flexibility, and improved profitability.
ERP systems provide centralized data management, advanced planning and scheduling tools, quality management features, and real-time inventory optimization.
Best practices include implementing lean manufacturing principles, embracing automation, investing in training, utilizing data analytics, and collaborating with suppliers.
Common KPIs include Overall Equipment Effectiveness (OEE), production cycle time, scrap rate, and on-time delivery rate. Monitoring these KPIs helps assess production performance and identify improvement areas.
Let’s discuss, we are here to accelerate your business and ROI