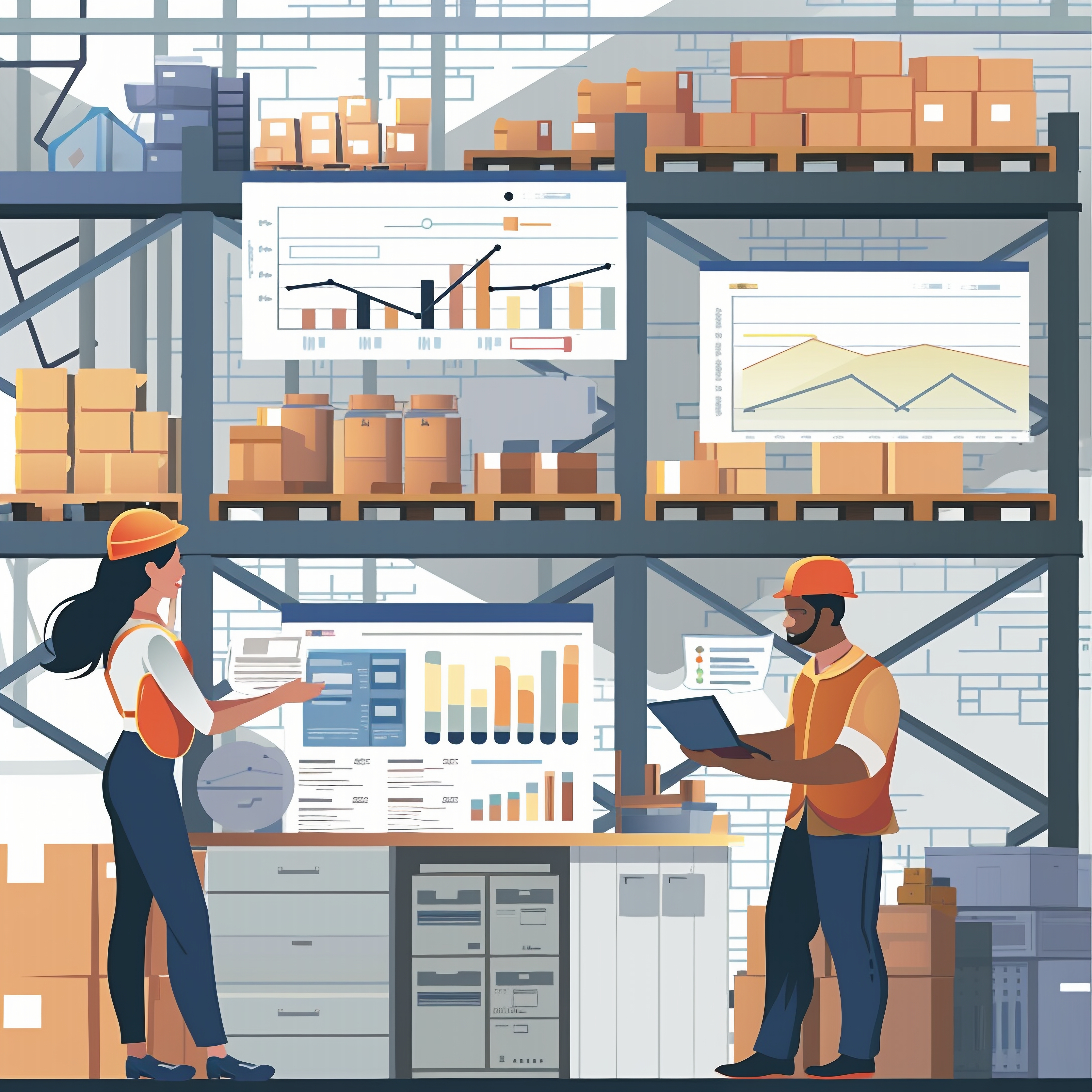
Scaling Operations with ERP: Multi-Location Inventory and Warehouse Management
As businesses expand, managing multiple locations and warehouses becomes increasingly complex. Efficiently tracking inventory, ensuring timely deliveries, and maintaining accurate records are just a few of the challenges that can arise. Enterprise Resource Planning (ERP) systems offer robust solutions to these problems, enabling seamless scaling of operations. This blog explores how ERP systems facilitate multi-location inventory and warehouse management, helping businesses grow and operate efficiently.
Understanding ERP and Its Importance
What is ERP?
Enterprise Resource Planning (ERP) systems are integrated software platforms that manage a company’s core business processes in real-time. These systems consolidate various functions, such as accounting, procurement, project management, and supply chain operations, into a single, cohesive system.
Why is ERP Important for Multi-Location Management?
When managing operations across multiple locations, it becomes crucial to have a unified system that provides visibility and control over all aspects of the business. ERP systems offer this by:
- Centralizing data for real-time access and decision-making.
- Standardizing processes across locations to ensure consistency.
- Enhancing coordination between different departments and sites.
- Improving resource allocation and utilization.
Key Features of ERP Systems for Multi-Location Inventory Management
Real-Time Inventory Tracking
One of the primary benefits of an ERP system is real-time inventory tracking. With multiple locations, it’s essential to know the exact inventory levels at each site to avoid stockouts or overstock situations. ERP systems provide:
Live updates: Automatic updates to inventory levels as goods are received, moved, or sold.
Visibility: A consolidated view of inventory across all locations, accessible from a single interface.
Alerts and notifications: Automated alerts for low stock levels, reorders, or discrepancies.
Warehouse Management System (WMS) Integration
ERP systems often include or integrate with Warehouse Management Systems (WMS), which are specifically designed to optimize warehouse operations. Key functionalities include:
Warehouse layout optimization: Efficient space utilization and easy location tracking.
Order picking and packing: Streamlined processes for picking, packing, and shipping orders.
Barcode and RFID scanning: Automated data capture for accurate inventory management and reduced human error.
Multi-Location Coordination
Managing multiple warehouses requires coordination to ensure that products are in the right place at the right time. ERP systems support this by:
Inter-warehouse transfers: Simplified processes for transferring stock between locations.
Demand forecasting: Predicting future inventory needs based on historical data and trends.
Centralized order management: Handling orders from all locations through a unified system to optimize fulfillment.
Advanced Reporting and Analytics
ERP systems provide powerful reporting and analytics tools to help businesses understand their operations better. These tools enable:
Comprehensive reports: Detailed reports on inventory levels, turnover rates, and order fulfillment.
Analytics dashboards: Visual dashboards that provide quick insights into key performance indicators (KPIs).
Data-driven decisions: Informed decision-making based on accurate, real-time data.
Benefits of ERP Systems in Multi-Location Inventory and Warehouse Management
Improved Efficiency
ERP systems streamline inventory and warehouse management processes, reducing the time and effort required to manage multiple locations. Automation of routine tasks minimizes human errors and frees up staff to focus on more strategic activities.
Cost Savings
By optimizing inventory levels and reducing excess stock, businesses can significantly lower carrying costs. Improved demand forecasting helps prevent stockouts and overstock situations, reducing waste and ensuring customer satisfaction.
Enhanced Customer Service
With real-time inventory visibility and efficient order fulfillment processes, businesses can ensure that products are available when and where customers need them. This leads to higher customer satisfaction and loyalty.
Scalability
ERP systems are designed to grow with your business. Whether you add new locations or expand your product lines, an ERP system can scale to meet your needs without requiring significant changes to your existing processes.
Compliance and Risk Management
ERP systems help businesses maintain compliance with industry regulations and standards. Automated record-keeping and audit trails ensure that all transactions are documented, reducing the risk of non-compliance and associated penalties.
Let's discuss, we are here to accelerate your business and ROI
Implementing an ERP System for Multi-Location Management
Assessing Your Needs
Before implementing an ERP system, it’s essential to assess your business needs and goals. Consider factors such as the number of locations, inventory volume, and specific challenges you face in managing multiple warehouses.
Choosing the Right ERP System
Select an ERP system that offers robust multi-location inventory and warehouse management capabilities. Look for features such as real-time tracking, WMS integration, advanced reporting, and scalability. Additionally, consider the system’s ease of use and the level of support provided by the vendor.
Planning the Implementation
A successful ERP implementation requires careful planning and execution. Key steps include:
Project team: Assemble a team of stakeholders from various departments to oversee the implementation.
Timeline and budget: Establish a realistic timeline and budget for the project.
Data migration: Plan for the migration of existing data to the new system.
Training: Ensure that staff are adequately trained to use the new system.
Continuous Improvement
Post-implementation, continuously monitor the system’s performance and seek opportunities for improvement. Regularly update the system to leverage new features and enhancements.
Best Practices for Multi-Location Inventory and Warehouse Management
Standardize Processes
To ensure consistency and efficiency across all locations, standardize inventory and warehouse management processes. This includes:
Documentation: Maintain comprehensive documentation for all procedures.
Training: Provide uniform training for staff across all locations.
SOPs: Develop Standard Operating Procedures (SOPs) for common tasks.
Leverage Technology
Utilize advanced technologies such as Internet of Things (IoT) devices, artificial intelligence (AI), and machine learning to enhance your ERP system’s capabilities. These technologies can provide:
Predictive analytics: Forecast future trends and inventory needs.
Automation: Automate routine tasks and improve accuracy.
Real-time data: Access real-time data from IoT devices for better decision-making.
Optimize Inventory Levels
Implement strategies to optimize inventory levels, such as:
Just-In-Time (JIT): Reduce inventory holding costs by receiving goods only as they are needed.
Safety stock: Maintain a buffer stock to mitigate the risk of stockouts.
ABC analysis: Categorize inventory based on importance and prioritize management efforts accordingly.
Enhance Communication
Effective communication is crucial for managing multiple locations. Ensure that there is clear and open communication between all sites by:
Regular meetings: Hold regular meetings to discuss performance and address issues.
Collaboration tools: Use collaboration tools to facilitate communication and information sharing.
Feedback loops: Establish feedback mechanisms to continuously improve processes.
Monitor Performance
Regularly monitor and evaluate the performance of your inventory and warehouse management processes. Use key performance indicators (KPIs) to track progress and identify areas for improvement. Some important KPIs include:
Inventory turnover ratio: Measures how often inventory is sold and replaced.
Order accuracy: Tracks the accuracy of order fulfillment.
Lead time: Measures the time taken from order placement to delivery.
Conclusion
Scaling operations across multiple locations and warehouses is a complex task that requires efficient management of inventory and seamless coordination between sites. ERP systems provide the tools and capabilities needed to achieve this, offering real-time visibility, advanced analytics, and automated processes. By implementing an ERP system, businesses can enhance efficiency, reduce costs, and improve customer satisfaction, all while positioning themselves for future growth.
As the business landscape continues to evolve, leveraging technology like ERP systems will be crucial for staying competitive and meeting the demands of an increasingly dynamic market. Whether you’re a small business looking to expand or a large enterprise seeking to optimize your operations, ERP systems can provide the foundation for successful multi-location inventory and warehouse management. Investing in the right ERP solution and following best practices will enable your business to thrive in a complex, multi-location environment.
FAQs
An ERP (Enterprise Resource Planning) system is an integrated software platform that manages a company’s core business processes in real-time, consolidating functions like accounting, procurement, project management, and supply chain operations into a single system.
ERP systems benefit multi-location inventory management by centralizing data for real-time access, standardizing processes across locations, enhancing coordination between departments, and improving resource allocation and utilization.
Key features to look for include real-time inventory tracking, Warehouse Management System (WMS) integration, multi-location coordination, and advanced reporting and analytics.
Real-time inventory tracking in an ERP system involves automatic updates to inventory levels as goods are received, moved, or sold, providing a consolidated view of inventory across all locations accessible from a single interface.
A WMS integrated with an ERP optimizes warehouse operations through efficient space utilization, streamlined picking and packing processes, and automated data capture using barcode and RFID scanning.
ERP systems improve efficiency by automating routine tasks, reducing human errors, and freeing up staff to focus on strategic activities, thereby streamlining inventory and warehouse management processes.
Cost savings include lower carrying costs by optimizing inventory levels, reducing excess stock, and improving demand forecasting to prevent stockouts and overstock situations, leading to reduced waste and increased customer satisfaction.
ERP systems enhance customer service by providing real-time inventory visibility and efficient order fulfillment processes, ensuring products are available when and where customers need them, leading to higher satisfaction and loyalty.
Steps include assessing business needs, choosing the right ERP system, planning the implementation (including forming a project team, establishing a timeline and budget, data migration, and staff training), and continuous improvement.
Best practices include standardizing processes, leveraging advanced technologies, optimizing inventory levels, enhancing communication, and regularly monitoring performance using key performance indicators (KPIs).
Let’s discuss, we are here to accelerate your business and ROI