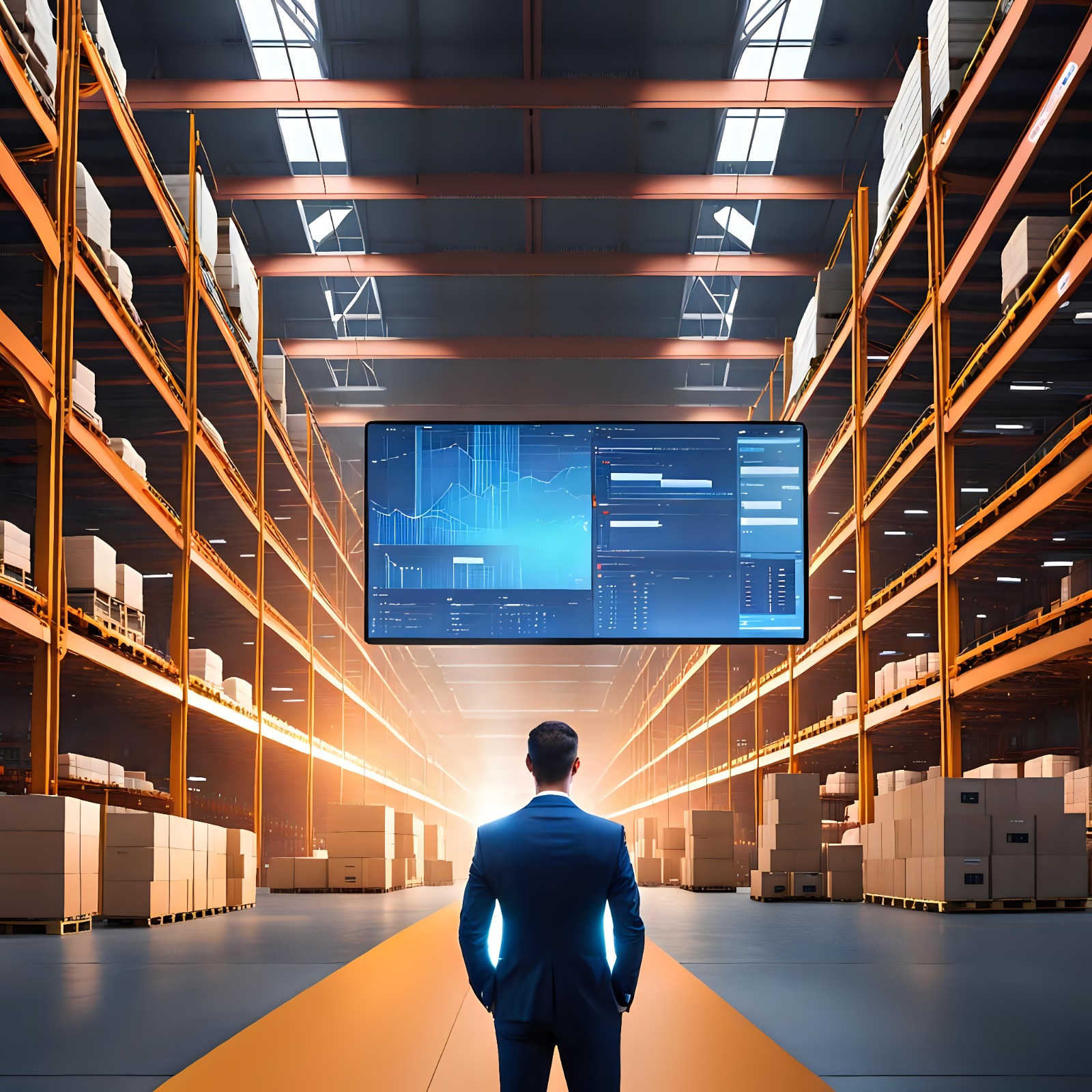
Inventory Management Techniques for Optimal Stock Control
Inventory management is a critical aspect of supply chain management that involves overseeing the flow of goods from manufacturers to warehouses and from these facilities to point of sale. Efficient inventory management is vital for businesses to maintain optimal stock levels, reduce carrying costs, and meet customer demand effectively. The intricacies involved in inventory management have led organizations to adopt various techniques to streamline operations and enhance productivity.
In this blog, we will delve into several inventory management techniques that can help businesses achieve optimal stock control. From leveraging technology to implementing effective methodologies, we will explore how organizations can enhance their inventory management practices to achieve better results.
Understanding Inventory Management
Inventory management encompasses the processes and systems used to oversee the ordering, storage, and utilization of a company’s inventory. This includes raw materials, work-in-progress items, and finished goods. Effective inventory management ensures that a business maintains the right amount of stock to meet customer demand without overstocking or understocking.
Key Objectives of Inventory Management
- Cost Reduction: Minimize holding costs associated with storing excess inventory.
- Stock Availability: Ensure that products are available to meet customer demand.
- Supply Chain Efficiency: Optimize the flow of goods through the supply chain.
- Improved Cash Flow: Free up cash tied up in excess inventory.
- Enhanced Decision-Making: Provide accurate data for informed decision-making.
Key Inventory Management Techniques
- Just-In-Time (JIT) Inventory Management
JIT is a strategy that aims to reduce inventory carrying costs by receiving goods only as they are needed in the production process. This approach minimizes the amount of inventory on hand, reducing storage costs and waste. However, JIT requires precise coordination with suppliers and an efficient logistics system.
Benefits of JIT:- Reduces waste and holding costs.
- Improves cash flow by lowering inventory levels.
- Increases responsiveness to customer demand.
- Challenges of JIT:
- Requires reliable suppliers and transportation.
- Vulnerable to supply chain disruptions.
- May not be suitable for all industries.
- ABC Analysis
ABC analysis categorizes inventory into three categories (A, B, and C) based on their value and importance to the business.- A Items: High-value items with a low frequency of sales (e.g., electronics).
- B Items: Moderate-value items with a moderate frequency of sales (e.g., clothing).
- C Items: Low-value items with a high frequency of sales (e.g., office supplies).
- This technique helps businesses prioritize inventory management efforts and allocate resources effectively.
Benefits of ABC Analysis:- Focuses attention on high-value items.
- Allows for tailored inventory management strategies.
- Enhances inventory turnover rates.
- Challenges of ABC Analysis:
- Requires ongoing analysis and categorization.
- May not capture the complexity of all inventory items.
- Economic Order Quantity (EOQ)
EOQ is a mathematical model used to determine the optimal order quantity that minimizes total inventory costs, including ordering and holding costs. This technique helps businesses identify how much to order and when to reorder.
The EOQ formula is:
EOQ=2DSHEOQ = \sqrt{\frac{2DS}{H}}EOQ=H2DS
where:- DDD = Demand rate (units per year)
- SSS = Ordering cost per order
- HHH = Holding cost per unit per year
- Benefits of EOQ:
- Balances ordering and holding costs.
- Reduces stockouts and overstock situations.
- Provides a systematic approach to ordering.
- Challenges of EOQ:
- Assumes constant demand and lead times.
- May not account for fluctuations in market demand.
- First-In, First-Out (FIFO) and Last-In, First-Out (LIFO)
FIFO and LIFO are inventory valuation methods that dictate how inventory is managed and sold.- FIFO: Assumes that the oldest inventory is sold first. This method is ideal for perishable goods and helps maintain fresh stock.
- LIFO: Assumes that the most recently acquired inventory is sold first. This method may be beneficial for businesses facing inflation as it can reduce taxable income.
- Benefits of FIFO and LIFO:
- FIFO prevents obsolescence of perishable goods.
- LIFO can provide tax advantages in inflationary periods.
- Challenges of FIFO and LIFO:
- May not accurately reflect actual inventory flow.
- Requires careful record-keeping for valuation purposes.
- Consignment Inventory
Consignment inventory involves a supplier placing goods in a retailer’s location but retaining ownership until the items are sold. This technique reduces the retailer’s inventory costs and risks while allowing suppliers to expand their market reach.
Benefits of Consignment Inventory:- Lowers financial risk for retailers.
- Increases supplier visibility in the market.
- Encourages collaboration between suppliers and retailers.
- Challenges of Consignment Inventory:
- Requires trust between suppliers and retailers.
- May complicate inventory management and tracking.
- Dropshipping
Dropshipping is a retail fulfillment method where a store doesn’t keep the products it sells in stock. Instead, when a store sells a product, it purchases the item from a third party and has it shipped directly to the customer.
Benefits of Dropshipping:- Minimizes inventory holding costs.
- Reduces financial risk associated with unsold inventory.
- Allows for a wider product range without upfront investment.
- Challenges of Dropshipping:
- Lower profit margins due to reliance on third-party suppliers.
- Less control over inventory quality and shipping times.
- Potential for stockouts if suppliers are not reliable.
- Inventory Forecasting
Inventory forecasting involves predicting future inventory requirements based on historical sales data, market trends, and seasonality. Accurate forecasting helps businesses maintain optimal stock levels and improve order accuracy.
Benefits of Inventory Forecasting:- Enhances inventory turnover rates.
- Reduces stockouts and overstock situations.
- Improves customer satisfaction through better product availability.
- Challenges of Inventory Forecasting:
- Requires accurate data collection and analysis.
- Can be affected by unpredictable market changes.
Let's discuss, we are here to accelerate your business and ROI
The Role of Technology in Inventory Management
The integration of technology in inventory management has transformed how businesses manage their stock. Various tools and software solutions enhance inventory control, including:
- Inventory Management Software
Dedicated inventory management software provides real-time visibility into stock levels, sales trends, and order management. Features often include barcode scanning, stock alerts, and reporting capabilities. - Enterprise Resource Planning (ERP) Systems
ERP systems integrate inventory management with other business functions, such as finance and supply chain management, providing a holistic view of operations. This integration improves decision-making and enhances overall efficiency. - Cloud-Based Solutions
Cloud-based inventory management solutions offer scalability and flexibility, allowing businesses to access data from anywhere and ensuring data security and backup. - Mobile Applications
Mobile apps enable businesses to manage inventory on the go, facilitating real-time updates and communication between teams. - Data Analytics
Advanced data analytics tools provide insights into inventory performance, helping businesses identify trends, forecast demand, and make informed decisions.
Best Practices for Optimal Inventory Management
To achieve optimal stock control, businesses should consider implementing the following best practices:
- Regular Inventory Audits
Conduct regular audits of inventory to identify discrepancies and ensure accurate stock levels. This helps in maintaining inventory integrity and minimizing loss. - Set Par Levels
Establish par levels, or minimum stock thresholds, for each product to ensure timely reordering and prevent stockouts. - Utilize Technology
Leverage inventory management software or ERP systems to automate processes, gain real-time visibility, and improve accuracy. - Train Staff
Provide training to staff involved in inventory management to ensure they understand best practices and utilize the tools effectively. - Review Supplier Performance
Regularly assess supplier performance to ensure they meet delivery timelines and quality standards, helping to maintain optimal inventory levels. - Implement Lean Inventory Practices
Adopt lean inventory practices to minimize waste and improve efficiency. This involves regularly reviewing inventory levels and eliminating excess stock.
Conclusion
Effective inventory management is crucial for businesses seeking to optimize stock control and enhance overall operational efficiency. By implementing proven techniques such as JIT, ABC analysis, and EOQ, businesses can achieve better inventory control and meet customer demand while reducing costs.
Moreover, leveraging technology, including cloud-based ERP systems, can streamline inventory processes and improve data accuracy. Partnering with the Best ERP Solution Provider in Hyderabad can offer significant advantages in optimizing inventory management practices. As the Best ERP services provider, we deliver the #1 Cloud-based ERP System to help your organization achieve optimal stock control and enhance operational efficiency.
FAQs
Inventory management is the process of overseeing the flow of goods and materials in a business, ensuring optimal stock levels and efficient operations.
Effective inventory management helps businesses reduce costs, enhance cash flow, meet customer demand, and improve overall operational efficiency.
Common techniques include Just-In-Time (JIT), ABC analysis, Economic Order Quantity (EOQ), FIFO (First-In, First-Out), LIFO (Last-In, First-Out), consignment inventory, dropshipping, and inventory forecasting.
Technology, such as inventory management software and ERP systems, enhances inventory control by providing real-time visibility, automating processes, and integrating various business functions for better decision-making.
Improving inventory turnover can be achieved by implementing demand forecasting, optimizing stock levels, conducting regular inventory audits, and utilizing effective inventory management techniques like JIT or ABC analysis.
Just-In-Time (JIT) aims to minimize inventory holding costs by receiving goods only when they are needed, while Economic Order Quantity (EOQ) determines the optimal order quantity that minimizes total inventory costs, including ordering and holding costs.
Inventory audits should be conducted regularly, with frequency depending on the business's size and complexity. Some businesses may benefit from annual audits, while others may need quarterly or monthly reviews.
Par levels are the minimum stock thresholds for inventory items. Setting par levels is important to ensure timely reordering, prevent stockouts, and maintain optimal stock levels.
While it’s possible to manage inventory manually, using software or an ERP system significantly enhances accuracy, efficiency, and visibility, making it easier to track stock levels, orders, and trends.
Cloud-based inventory management systems offer scalability, flexibility, real-time access to data from anywhere, data security, automatic updates, and reduced IT maintenance costs.
In consignment inventory, a supplier places goods at a retailer's location but retains ownership until the items are sold. This arrangement minimizes the retailer's inventory costs and risks.
JIT inventory management can pose challenges such as reliance on reliable suppliers, vulnerability to supply chain disruptions, and the need for precise coordination in logistics.
Seasonal demand can significantly impact inventory management. Businesses should adjust their inventory levels and forecasting techniques to accommodate fluctuations in demand during peak and off-peak seasons.
Data analytics can provide insights into sales trends, customer behavior, and inventory performance, enabling businesses to make informed decisions, optimize stock levels, and improve forecasting accuracy.
To address excess inventory, businesses can consider implementing discounts, promotions, bundling products, or donating items to reduce stock levels and free up cash.
Let’s discuss, we are here to accelerate your business and ROI